Or, as Bruce Roberts titled it, “Our Coal Mine Is the Canary.”
I’m a career investment banker who now also owns and operates several Appalachian coal mines.
This isn’t a piece defending coal – though you might find it surprising, if not more than a little ironic, to know that you can’t make a solar panel, or an electric vehicle, without metallurgical-grade coal, like ours.
While canaries aren’t used in the mines anymore, coal mining, in the broader sense, reflects our national condition. That is, just how far the U.S. manufacturing sector has fallen in the past 40 years. When I took control of our mines a few years ago, I had no idea of the day-to-day challenges I would face, or that most of them aren’t unique to coal mining.
So, I thought I’d give you a real-world peek at what’s happening at the ground level (and in our case, also underground).
Reshoring … Tougher than You Might Think
For over 30 years, the world has taken a vacation from “sovereign risk” and gone global like never before. Unfortunately, countries are at each other’s throats again, and U.S. companies are compelled to “reshore.” A recent Deloitte survey of U.S. manufacturers found that over 62% have started reshoring or near-shoring their production capacities.
Reshoring, bringing manufacturing back to within the borders of the United States, isn’t going to happen as easily as you might expect. That is, unless you’ve previously managed a production line along with the inputs needed to keep it running, and you appreciate just how perfect a world it takes to keep it running. As a banker for most of my 40-year career, I hadn’t experienced it. But I sure get it now …
2023 isn’t 1983. After decades of outsourced “fulfillment” around the planet via “globalization,” the U.S. is now facing the consequences, especially if you’re actually trying to produce something in a physical form and not just running a blockchain, exploiting an algorithm, or crafting some SaaS application.
“Digging” Deeper
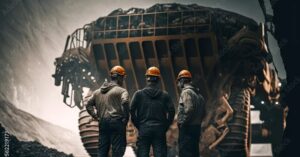
Skilled employees – difficult to find
America’s manufacturing challenges include the following.
Hiring Employees – A generation of skilled workers and much of the apprenticeship system needed to generate them have been lost. We have lots of web page designers and lawyers, but we’re short of folks who can operate industrial machinery or repair high-voltage electrical equipment.
Furthermore, most jobs require crews to show up at a specific location and time to work as a team, like our nine-man crews that operate our continuous mining coal-extraction machines. A range of complementary skills is needed across the crew. Even if you can put one together, there are few, if any, backup workers, and, if someone is out sick (e.g., COVID), the crew is down and we produce no coal.
Finding Equipment – America no longer leads in the production of “machine tools,” equipment that is essential for production lines. According to the Rand Corporation, U.S. machine tool manufacturing dropped from being the worldwide leader in the early 1980’s to a distant number four today (just behind Italy). Machine tooling is the bedrock for all types of manufacturing lines.
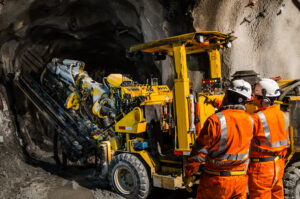
Stockpiling parts is critical
Getting Spare Parts – Too many of the providers of specialty replacement parts are either gone or hanging on with aging owners and workers. Need a machine shop to fabricate a new hydraulic line or torque shaft? Good luck. Manufacturers now need to be vertically integrated like they were 100 years ago when the machine shop was in-house.
Sourcing Raw Materials – A stable manufacturing industry starts with reliable sources of raw materials. The U.S. has prioritized domestic microchip manufacturing, but this production will still be dependent on foreign countries for silicon metal. In 2019, the U.S. produced 4.6% of the world’s silicon metal, while Russia and China together produced 72.8%. This mismatched and vulnerable scenario is common to many products, including flat-screen monitors and batteries.
Logistics – Manufacturing always involves moving stuff around. FEDEX and Amazon are great for delivering something small directly to your house, but try moving 10,000 tons of coal, or 100,000 gallons of cooking oil, or anything else that can’t be moved efficiently by truck.
Rail transportation is four times more efficient than trucks, and I have a much better appreciation for rail lines and their relationship to industry. About 13.5% of the U.S. rail system has now been turned into hiking trails, with another 5% targeted for conversion.
Furthermore, the U.S. rail service isn’t what it used to be, or now needs to be. In April 2022, the situation became so dire that the U.S. Surface Transportation Board in Washington, DC held emergency hearings. This session was particularly enlightening, where a senior yardmaster detailed the many challenges he faces in providing dependable service.
Is the Situation Hopeless?
Absolutely not! At least not for the United States, given its many strengths, including enormous energy and natural resources, a vibrant population, and our capitalist system.
Private capital is also abundantly available for investment by wealthy individuals, family offices, and private funds, providing venture capital for start-ups and growth capital for more mature businesses.
But we have to:
- Be realistic about the extent of the enterprise and resources that are needed to fully support our domestic manufacturing, including the necessary supply chains, logistical support, and other infrastructure.
- Appreciate that this will take focus, capital, and time, just like it did in the 100 years preceding the time when America was the leading manufacturer in the world.
In short, manufacturing has to become cool in America. If it does, we are entering an exciting and highly productive period in American history.
If you are interested in direct private investments, I invite you to look here.
As published in forbes.com